Strandbeest XXL
Unser Strandbeest. In groß. Und aus Holz
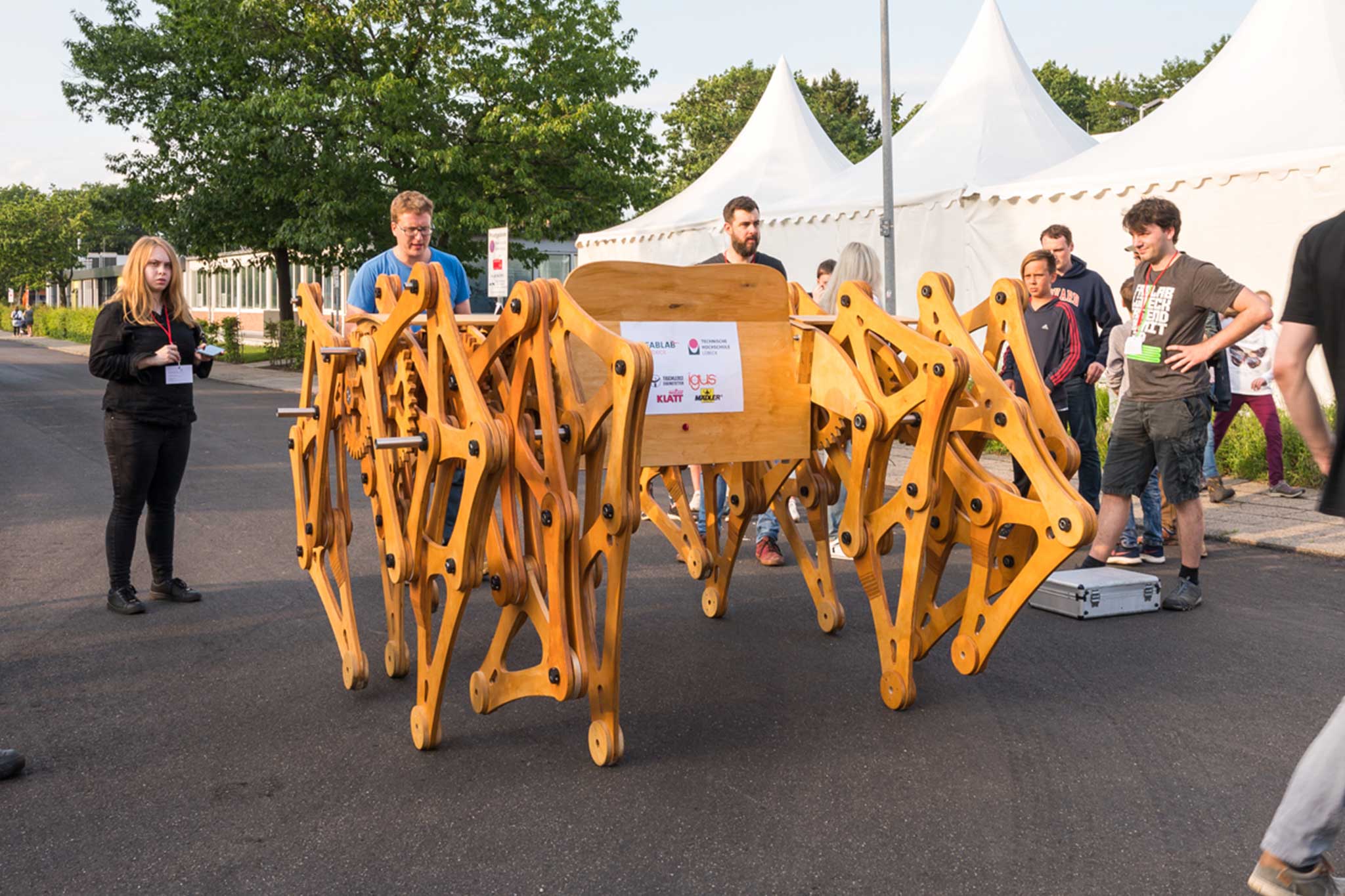
Projekt „Strandbeest Maximus“ – Schönheit, Anmut und Bionik in Technik vereint
Im Januar 2019 entstand die Idee zu einem Großprojekt, das all die vielseitigen Kompetenzen des FabLabs Lübeck vereinen sollte. Inspiriert durch die autonom laufenden, kinetischen Kunstobjekte, der sog. „Strandtiere“, des niederländischen Künstlers Theo Jansen, entstand die Idee zum Strandbeest Maximus. Angetan von der Idee der interdisziplinären Zusammenarbeit und der Sichtbarmachung dieser Kompetenzen in einem technisch komplexen Roboter mit Wow-Effekt, beschloss die TH Lübeck, dieses Projekt zu fördern.
Von da an bauten über ein Dutzend enthusiastische Mitglieder des FabLabs Lübeck am „Beest“. In nur 5 Monaten wurde aus einer vagen Vorstellung ein „Krabbler“ mit beachtenswerten Ausmaßen von 2 x 2 x 1,4 Metern, ca. 200 kg schwer, angetrieben von zwei Motoren 24 V Motoren je 450 W, ferngesteuert und mit einem zweiten Sicherheitssystem ausgestattet.
Die große Herausforderung des Konstruktionskünstlers lag in dem Entwurf eines sich anmutig bewegenden und doch technisch stabilen Modells aus Holz. Nur die Skizzen der Beinkonstruktion und deren Mechanik als Vorlage entwarf ein Vereinsmitglied das Modell am Computer. Da weder das Endgewicht des „Beestes“ noch die mechanischen Kräfte genau bekannt waren, mussten Erfahrungswerte angenommen werden. Hierbei zeigte sich die Vielfalt der verschiedenen Berufe, das Spektrum aus studentischen Theoriekenntnissen gemischt mit dem „groben Daumen“ der Berufserfahrenen als positive Mischung. Voller Erwartung und Freude wurde der erste CAD-Entwurf des animierten Modells Mitte Februar vom Team aufgenommen.
Es gab viele Diskussionspunkte. Macht ein „richtiges“ FabLab alles selbst oder sollten wir Kooperationen eingehen. Da wir einige Teile selbst an unserer Fräse gefräst hatten, wussten wir, dass wir es können. Doch wegen des Zeitdrucks nahmen wir die Unterstützung der Tischlerei Eigenstetter aus Rehna gerne an. In der ersten Aprilwoche war es dann soweit. Das erste Beinpaar war gefräst und zusammengebaut. Als unser Konstrukteur die Beine erstmals bewegte und bemerkte: „Hervorragend! Ich hätte nicht gedacht, dass das so gut geht.“, fielen uns viele Steine vom Herzen. Aber es stand uns noch viel Arbeit bevor.
Im Mai unterstützte uns Prof. Kral vom Fachbereich Maschinenbau und Wirtschaft der TH Lübeck. Er berechnete zusammen mit einem Studenten die auftretenden Kräfte und die somit notwendigen Materialstärken von 18 mm starkem, verleimtem Buchenholz. Wir waren stolz und froh, dass seine Berechnungen mit unseren Konstruktionen übereinstimmten und gaben die endgültigen Fräsarbeiten bei der Tischlerei Eigenstetter frei. Nach Ostern kamen die fertigen Teile aus der Tischlerei und es begann die Arbeit des Malens, des Schneidens der Lagerrohre, des Auslaserns von Beilagscheiben aus Acryl und des Zusammenbaus der Teile. Gleichzeitig begann ein weiteres Team sich mit der Elektronik und Fernsteuerung zu beschäftigen. 144 Gelenke mit 288 Beilagscheiben und Befestigungsschellen wurden montiert. Schlussendlich wurde das Mittelteil konstruiert und gebaut. Danach folgte die Antriebs-, die Regelungstechnik und die Fernsteuerung. Es handelt sich um ein zweifach abgesichertes System mit vier Sicherheitsstufen, deren Bau durch einen Elektriker überwacht wurde.
Nicht nur die Ausmaße des Strandbeests sind enorm. In 5 Monaten hat das Projektteam mehr als 400 Stunden in das Projekt investiert und viel gelernt. So kann z.B. ein fachfremdes Vereinsmitglied, das vorher nie Kontakt mit einer komplizierten CNC-Fräse hatte, jetzt eigenständig Teile fräsen. Trotz Auseinandersetzungen und Rückschlägen war es das alles wert. Bei aller Freude wollen wir auch unsere Dankbarkeit gegenüber unseren Unterstützern aussprechen. Das gemeinsame Projekt des Vereins Fablab Lübeck e.V. mit der TH Lübeck wurde zudem von Firmen unterstützt. Insbesondere sind wir dankbar, dass die Vereinsleitung und die übrigen Vereinsmitglieder uns die Möglichkeit eingeräumt hatten, unsere Werkstätten solange durch ein so enormes Projekt zu beschlagnahmen.
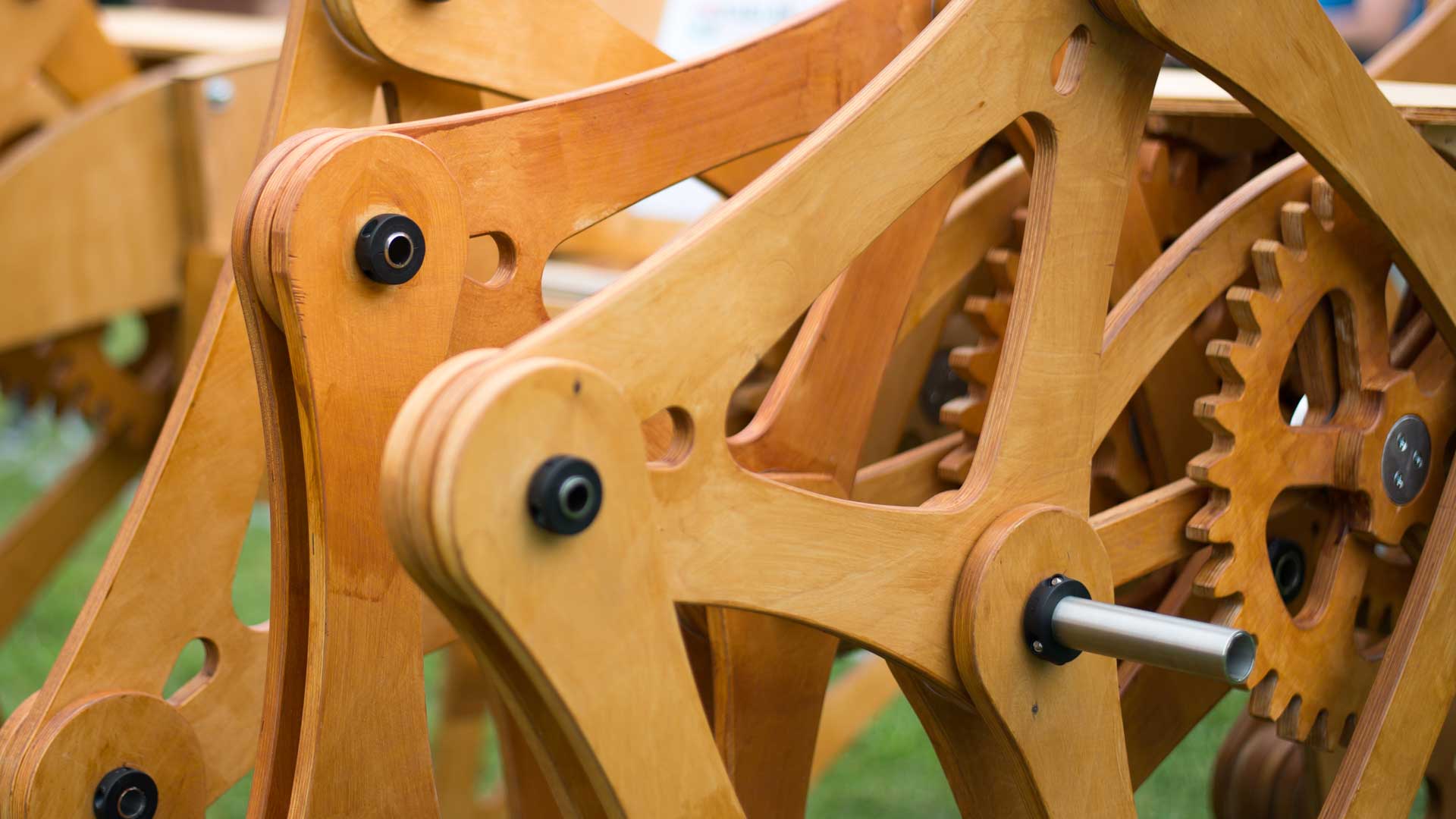
Projektleitung: Dr. Claus Schuster, Philip Kiefer
Projektkoordination, Controlling und Dokumentation: Jana-Melina Augener
Mechanisch-technische Koordination: Martin Hamann
Elektronisch-technische Koordination: Marco Gabrecht, Ian Pösse, Andre Scholze
Bau und Umsetzung: Philip Kiefer, Kilian Kreuzinger, Natascha Koch, Gina Seewald u.a.
Fotos: Bjarne Andersen
Kooperationen:
Tischlerei Eigenstetter, Rhena (https://www.eigenstetter.com/)
Fachbereich Maschinenbau und Wirtschaft der THL (Prof. Dr.-Ing. Roland Kral)
Sponsoring:
Firma MÄDLER GmbH (https://www.maedler.de/)
Firma IGUS (https://www.igus.de/)
Projektdauer: 5 Monate (15.1. – 15.6.2019)
Projektkosten: ca. 5500,-€ Materialkosten, ca. 400 Std. Arbeitszeit
Größe: 2m x 2m x 1,4m (BxTxH) m, 6 Gelenke/Bein, 12 Beine, jeweils 3x2 Beine pro Seite, 144 Gelenke (Metallrohre) und 288 Schellen
Material: 18 mm starkes, verleimtes Buchenholz, gefräst
Antrieb und Steuerung: Zwei 24 V Motoren je 450 W, Arduino steuert eine 100A H-Brücke, zweites Sicherheitssystem mit einem ATiny, der das Signal zur Fernbedienung prüft und den Strom unterbrechen kann. Übersetzung 1:10 mittels T10 Ritzel und Riemen